The Importance of Safety Devices in Industrial Automation
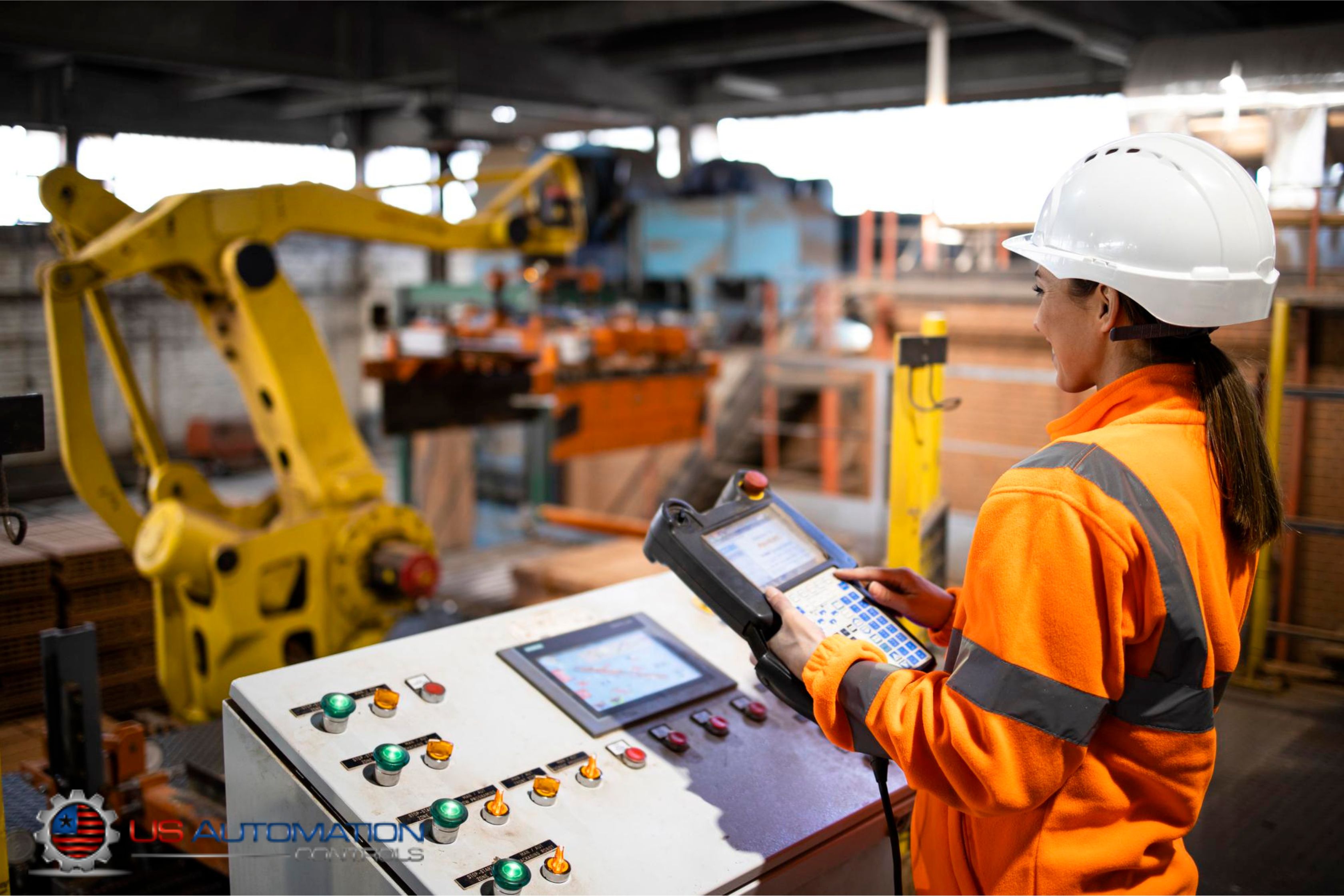
Industrial automation has revolutionized manufacturing and production by enhancing efficiency, reducing human error, and lowering operational costs. However, with these advancements come significant safety concerns. As automation advances, so does the complexity of industrial systems, leading to potential safety concerns. To prevent any accidents, safety measures are implemented in the form of safety switches. These switches aim to create a safe and healthy work environment and prevent any accidents from happening.
How A Safety Switch Works
Safety switches, also known as safety devices, monitor set parameters and take action if those parameters are not met. A simple example of a safety switch in a device is found in some table saws. These saws emit an electrical current through the sawblade. If anything conductive, like a hand, touches the sawblade, it closes a circuit. The switch detects this connection and sends a signal to the brakes, which immediately stops the blade. This concept works so well that the worst possible outcome is a flesh wound and, in most cases, a simple surface-level cut that will heal in no time.
Another example is the safety sensor on a treadmill. In this example, the operation of the safety sensor can be divided into four steps:
Monitoring
Safety switches monitor preset conditions that they were designed for, such as an electrical connection to a certain point or a mechanical factor like a door being closed. They continuously monitor these factors until they are altered.
In the treadmill, the switch sends an electrical signal and checks to see if that circuit is completed. For this connection to be made, the safety clip of the treadmill should be inserted. If the switch detects that this connection is made, it means the clip is in the treadmill and everything is operating as normal.
Action
When a condition is no longer met, the switch immediately sends a signal to the output, activating a safety mechanism. This safety mechanism can vary from device to device and application to application.
If the clip is ripped out of the socket due to slipping, falling, or any other reason, the switch detects that the connection is no longer made, meaning the clip is not in place and the safety conditions are not met. The switch sends a signal to the treadmill controller board, instructing it to stop its operation.
Shutdown
After the safety mechanism receives this activation signal, it kicks into action. A safety mechanism can be designed to shut down the machine, like how the sawblade stops in place, or it can deploy a cautionary measure, like an alarm. After the controller board receives this signal, it follows protocol and stops the treadmill track, preventing the user from suffering further damage from being scraped by the track.
Restoring Safety
Now that the switch has taken action, it switches its role. The switch constantly checks to see if the conditions are met again. The switch will continue to search for these conditions until they are met, at which point it goes back to normal operation.
The switch will now check for the clip until it is inserted again. In the meantime, the treadmill track cannot move because the safety conditions are not met.


Why Safety Devices Matter in Industrial Automation
Protecting Human Lives and Preventing Injuries
The primary purpose of safety devices in industrial automation is to protect lives and prevent injuries. Industrial environments can be hazardous, with heavy machinery, high voltages, and dangerous processes all over the place; safety should be a top priority. Safety devices, such as emergency stop buttons or interlock switches, are designed to mitigate these risks by immediately halting operations in case of an emergency or unsafe condition. This rapid response is crucial in preventing accidents and ensuring the well-being of workers.
Ensuring Compliance with Regulations and Standards
Industries are subject to strict safety regulations and standards, such as those set by the Occupational Safety and Health Administration (OSHA). Compliance with these standards is mandatory, and failure to adhere can result in severe penalties, legal consequences, and damage to a company's reputation.
Enhancing Operational Efficiency
While the primary focus of safety devices is to prevent accidents, they also contribute to enhancing operational efficiency. By minimizing the risk of accidents and unplanned downtime, safety devices ensure that production processes run smoothly. This not only maintains productivity but also reduces costs like equipment damage.
Protecting Equipment and Investments
A safety switch does not just protect employees; it also protects the machines. These machines and devices are a significant investment for companies. Safety devices protect these investments by preventing damage to machinery and equipment. In many cases, devices can malfunction by themselves and end up damaging other parts of the device. Safety sensors prevent a machine from causing damage to both itself and the employee operating the device.
Implementing Safety Devices
Conduct a Thorough Risk Assessment
The first step in implementing safety devices is to conduct a comprehensive risk assessment of the industrial environment. Identify all potential hazards and assess the likelihood and severity of accidents. This assessment will help determine the appropriate safety devices and their placement.
Choose the Right Safety Devices
Select safety devices that are suitable for the specific hazards identified in the risk assessment. Consider factors such as the type of machinery, the nature of the processes, and the level of risk.


Integrate Safety Devices into the Control System
Integrate safety devices into the industrial control system to ensure seamless operation. Safety relays and controllers play a crucial role in this integration, ensuring that safety devices function correctly and can trigger a shutdown if necessary. Proper integration ensures that safety devices do not interfere with normal operations and provide reliable protection.
Regularly Inspect and Maintain Safety Devices
Regular inspection and maintenance of safety devices are essential to ensure their continued effectiveness. Establish a maintenance schedule and conduct periodic checks to ensure that safety devices are functioning correctly. If a faulty safety switch is found, it should be replaced immediately.
Train Employees on Safety Procedures
A critical part of any safety system is employee training. Employees need to understand and follow protocols in case of an emergency. The last thing you want in the event of an emergency is somebody walking into a dangerous area and getting injured or someone making things worse while trying to help. Every employee needs to be trained on the proper use of machinery and safety devices, and what to do when those safety devices get triggered.
Should You Implement Safety Switches?
In short, yes. Safety systems are an essential part of any industry. Safety devices are indispensable as they ensure that every part of your operation is running smoothly. By understanding the importance of safety devices and implementing them effectively, industries can create a safer, more productive, and compliant working environment.
So if you are asking yourself if you need them, the answer is yes, you probably do, and luckily you are in the right place. Us Automation Controls is here to provide you with all your industrial safety switch needs with our vast array of safety products.
Make the call and make your workspace a safer and more efficient environment today!